Ceramic composites
Details
With the development of fiber preparation technology and other related technologies, the effective methods to prepare such materials have been gradually developed. It has made the preparation technology of Continuous-Fiber-Reinforced Ceramic Matrix Composite more and more mature. At present, Continuous-Fiber-Reinforced Ceramic Matrix Composites have been widely used in aerospace, national defense and other fields.
Continuous-Fiber-Reinforced Ceramic Matrix Composites have been widely used in the field of aerospace.
Silicon carbide fiber (SiCf) / silicon carbide ceramic (SiC) matrix composites have become a new generation of high temperature resistant materials for Aeroengines. High temperature components of aero-engine mainly include combustion chamber, high or low pressure turbine and nozzle and so on. Among them, high or low pressure turbine components mainly include guide blades, rotor blades and turbine outer rings. In the past, these components were mainly made of superalloys. Its temperature resistance limit is maintained at about 1100 ℃. However, the application of SiCf / SiC ceramic matrix composites improves the temperature resistance of engine components to 1200 ~ 1350 ℃. The components quality of ceramic matrix composites is usually 1/4 to 1/3 times that of superalloys. This not only achieves fuel economy, but also improves fuel economy.
The main preparation technique of SiCf/SiC composites include chemical vapor infiltration (CVI), polymer immersion cracking (PIP) and melt siliconization (MI). In 2015, GE company in US adopted the prepreg infiltration technique to prepare SiCf / SiC composites. SiC fibers can be converted into finished products of any shape in less than 30 days. GE Company successfully verified the world's first rotating low-pressure turbine component on the f414 turbofan engine verification machine. This indicates that the continuous fiber reinforced ceramic matrix composites have a wide application prospect in aeroengines and gas turbines. In May 2021, the first adaptive variable cycle engine xa100 of GE Company was tested. Ceramic matrix composite materials are widely used in this engine, which will provide power for the sixth generation fighter of US. In the 1980s, Safran Group in France began to use CVI Process to prepare rotor blades, mixers and center cones made of SiCf/SiC composite materials. They have been tested on CFM56 engine in the ground test. In addition, the nozzle components have also been flight verified on A320, A380 and other aircraft. The passing of airworthiness certification marks the advent of the era of using SiCf/SiC composite materials for high-temperature components of aeroengines.
Ceramic matrix composites are the key thermal protection materials for the safe flight of hypersonic vehicles. The flight speed of a hypersonic vehicle is greater than or equal to 5 times the speed of sound. In such a high-speed flight, it is necessary to ensure that the key structural components of the vehicle will not be damaged due to intense air friction and hot air flow impact up to 2000 ~ 3000 ℃.
Fiber-Reinforced Ceramic Matrix Composites have many advantages, such as excellent high temperature performance, high toughness, high specific strength, high specific modulus and good thermal stability, which can effectively overcome the sensitivity to cracks and thermal shock. It also has important applications and a wide market in the field of reusable thermal protection. At present, ceramic matrix composite thermal insulation materials have been developed from a single material to a new thermal protection system combining materials and structures. At the same time, it also develops from the traditional design of heat protection, heat insulation and load-bearing separately to the light direction of heat protection, heat insulation and load-bearing integration.
Fiber-Reinforced Ceramic Matrix Composites have many excellent properties such as high temperature resistance, ablation resistance, high strength, low dielectric, low loss and high reliability. They should be the key material of radome, which is one of the bottlenecks and difficult technologies in the development of new missiles and combat aircraft. At present, there are mainly composites such as quartz, fiber-reinforced quartz ceramics, quartz fiber-reinforced silicon nitride ceramics, nitride fiber-reinforced silicon nitride ceramics and so on. They all have excellent comprehensive properties such as high temperature resistance, wave transmission, bearing & heat release and so on. During the period from 2016 to 2020, Shandong industrial ceramics research and Design Institute Co., Ltd., has carried out systematic research on continuous nitride fiber fabric and nitride chopped fiber reinforced silicon nitride composite system. The composite material developed by the company has excellent ablation resistance, excellent dielectric properties and good mechanical properties. Under the condition of high heat flux and enthalpy, it can withstand high temperature of 2700 ℃ and long-term ablation test. It should be a new generation of ceramic wave transmitting composite material that can meet the requirements of high speed, long endurance, low ablation and high wave transmission in the future.
It has developed rapidly in the civil field.
Application in brake system
C/C-SiC composites have been used in brake systems, as the material has low density, good wear resistance, constant and stable friction coefficient, thermal shock resistance, oxidation resistance and other advantages. This kind of brake disc is light in weight, high in temperature resistance and 2.5 times higher in specific heat capacity than steel. Compared with the metal brake system, this brake disc can save 40% of the structural weight. The service life of carbon brake disc is 5-7 times that of metal base. Especially, its braking torque is stable and the noise is small when braking. C/C-SiC composites carbon brake disc has been applied in practical situations.
Application in biology
C/C composites material is a new potential biomedical material, which has a good application prospect in human bone repair and bone replacement. At present, C/C composites material have been used in pelvis, bone splint and bone needle in clinic field. It has also been reported that this material is used as a repair material for the middle ear of artificial heart valves. It has also achieved good clinical application effect in artificial root.
Application in heating element
Graphite heat generator is low in strength, brittle and difficult to process and transport. C/C composites material have the advantages of high strength, good toughness, high temperature resistance, and so on. This material can reduce the volume of heating body, expand the working area and so on.
Application in the field of environmental protection
Shandong industrial ceramics research and Design Institute Co., Ltd., has successfully developed a new type of ceramic fiber composite functional membrane tube in recent years. This composite material is a high-temperature gas purification material that integrates high-efficiency particle purification and catalytic denitration functions, which can effectively remove soot particles and nitrogen oxides at high temperature (above 250 ℃). such kind of material has the advantages of high filtration efficiency, high temperature resistance, good high-temperature catalytic activity, high NOx conversion efficiency, long service life and so on. Its filtering precision can intercept 0.1μm particles and its lowest emission is 1mg/m³. Its temperature resistance is as high as 650 ℃. Especially, its nitrogen oxide removal rate can reach more than 97%. Ceramic fiber composite functional membrane has been widely used in high-temperature gas purification in building materials, incineration, coking, biomass power generation and other fields.
Till now, there are still many technical difficulties to be overcome.
The research of ceramic matrix composites in China started relatively late. However, the substantial breakthroughs have been made in recent years. In terms of high-performance ceramic fibers, the main fibers such as silicon carbide, aluminum oxide, silicon nitride, nitride and others have achieved breakthroughs in engineering technology and industrialization. Preparation technology, processing technology, connection technology, reliability evaluation technology and application technology of ceramic matrix composites have been greatly improved. Many components of aeroengines have been designed, developed and evaluated. However, there is still a big gap in the comparison with the advanced countries such as Europe, America, Japan and so on. In terms of component assessment verification and application, China is still in its infancy. The application scope and cumulative assessment time are very limited. There is also a huge gap compared with foreign engineering application research.
In order to realize the application of ceramic matrix composites in high-temperature components of aeroengines, there are following technical difficulties needing to be mainly solved:
1) to develop high-performance ceramic fibers represented by ultra-high temperature and low-cost carbide fibers and their composite technology;
2) to break through silicon carbide, aluminum oxide, silicon nitride, boron nitride, silicon boron nitrogen and other fibers and the engineering stable preparation technology of its precursor;
3) to develop rapid and low-cost manufacturing technology of ceramic matrix composites;
4) to break through the key technologies in the whole industrial chain of ceramic matrix composites, and achieve effective coordination of related technologies;
5) to strengthen research on intrinsic structure and failure mechanism of ceramic matrix composites, and establish life prediction model;
6) to strengthen the research on the application side and establish the evaluation system and standards;
In present market, ceramic matrix composites with high application demand in the market mainly include silicon carbide fiber reinforced silicon carbide ceramic matrix (SiCf/SiC) and carbon fiber reinforced silicon carbide ceramic matrix (CF/SiC) composites. Among them, the former is considered to be one of the most promising materials for the future aero-engine, which is also the key material to improve the performance of the aero-engine. In the future, the development potential of domestic ceramic composite material market is huge.
Ceramic Matrix Composite (CMC)
Definition
Composites can be divided into three categories according to the different substrates:
Polymer Matrix Composite (PMC)
Metal Matrix Composite (MMC)
Ceramic Matrix Composite (CMC)
Among them, the application of PMC plays a leading role in aerospace. The mentioned composite materials will be associated with terms such as thermosetting plastics, CFRP (carbon fiber reinforced polymer based composite) and so on.
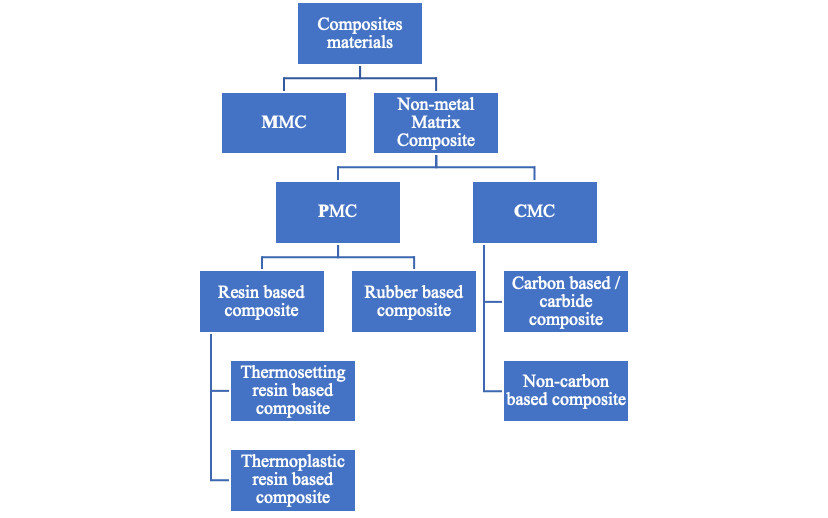