Aplicaciones de la Cerámica Avanzada en el Campo de los Materiales Resistentes al Desgaste
La industria de resistencia al desgaste y la corrosión es una rama de la industria de tratamiento de superficies.Como industrias emergentes de cuidados preventivos y servicios de tecnología de remanufactura, son muy importantes para resolver los problemas de desgaste y corrosión de equipos y piezas de trabajo en las industrias de energía, acero, minería química, cemento y otras.La industria resistente a la abrasión y la corrosión tiene una gran vitalidad.La vida útil de los equipos industriales se puede mejorar en gran medida mediante la protección contra el desgaste y la corrosión.Al mismo tiempo, se puede reducir el consumo de acero y otros materiales causados por el mantenimiento o la sustitución para ahorrar recursos.La industria resistente al desgaste y la corrosión es una medida importante para ahorrar recursos, proteger el medio ambiente y promover la economía circular.También son poderosos asistentes para que las empresas logren la conservación de energía y la reducción de emisiones, reduzcan costos y mejoren la eficiencia económica.
El núcleo de la industria de resistencia al desgaste y la corrosión es la aplicación de nuevos materiales y tecnologías en industrias relacionadas.Incluye principalmente tecnología cerámica resistente al desgaste, rociado térmico, superficie y placa resistente al desgaste, revestimiento láser, tecnología de revestimiento anticorrosión y resistente al desgaste, tecnología anticorrosión, tecnología de materiales resistentes al desgaste, etc.
Aplicaciones de la Cerámica Avanzada en el Campo de los Materiales Resistentes al Desgaste
Según las estadísticas, la fricción consume alrededor de 1/3 de la energía primaria del mundo.Mientras tanto, alrededor del 80% de las piezas de la máquina fallan debido al desgaste.La falla por desgaste de las piezas mecánicas está estrechamente relacionada con la selección de los materiales del par de fricción y las condiciones de servicio.En general,
►Los materiales resistentes al desgaste se refieren a los materiales utilizados en condiciones de fricción y desgaste con una pequeña cantidad de desgaste.
►Los materiales antifricción se refieren al material con pequeño coeficiente de fricción.
►Los materiales de fricción se refieren al material con gran coeficiente de fricción.
Es muy importante seleccionar y utilizar correctamente los materiales adecuados en función de las diferentes condiciones de trabajo y el rendimiento de fricción y desgaste que requieren las piezas mecánicas.Por ejemplo, los materiales resistentes al desgaste utilizados en ambientes de alto impacto son generalmente acero con alto contenido de manganeso.Sin embargo, en el entorno de carga de impacto pequeña, el uso de acero con alto contenido de manganeso no aprovechará las ventajas del endurecimiento por deformación del acero con alto contenido de manganeso, mientras que el uso de hierro fundido con alto contenido de cromo es más apropiado.No importa los materiales antifricción o los materiales de fricción, ambos deben tener una buena resistencia al desgaste al mismo tiempo.La buena resistencia al desgaste de los materiales no solo puede prolongar la vida útil de las piezas mecánicas, sino también reducir el reemplazo de piezas y la intensidad de trabajo de los trabajadores.Especialmente, la buena resistencia al desgaste de los materiales también puede ahorrar energía y recursos materiales.por lo tanto, es importante seleccionar correctamente los materiales resistentes al desgaste para mejorar el rendimiento del equipo mecánico y ahorrar energía en función de las diferentes condiciones de trabajo y los requisitos de rendimiento de las piezas mecánicas.
Tipos de materiales resistentes al desgaste.
Hay varios materiales resistentes al desgaste en el mundo.
•Según sus composiciones químicas, los materiales resistentes al desgaste se pueden dividir en materiales resistentes al desgaste de metal, materiales resistentes al desgaste de cerámica, materiales resistentes al desgaste de polímeros y compuestos resistentes al desgaste.
•Sobre la base de diferentes estructuras de materiales, los materiales resistentes al desgaste se pueden dividir en materiales integrales resistentes al desgaste y materiales resistentes al desgaste superficial.
•Según las diferentes temperaturas de uso, los materiales resistentes al desgaste se pueden dividir en materiales resistentes al desgaste a temperatura normal y materiales resistentes al desgaste a alta temperatura.
1) Materiales metálicos
Los materiales metálicos se pueden dividir en acero resistente al desgaste y hierro fundido resistente al desgaste.Los materiales metálicos comúnmente utilizados en la producción son acero de aleación resistente al desgaste, acero con alto contenido de manganeso, acero para cojinetes y acero para herramientas.La resistencia al desgaste del acero con alto contenido de manganeso mejora mediante el endurecimiento por deformación.Además, otros aceros resistentes al desgaste mejoran principalmente la dureza y la resistencia al desgaste del acero al agregar elementos formadores de carburo y formar carburos con carbono.En la actualidad, la tendencia de desarrollo del acero resistente al desgaste es el fortalecimiento de microaleaciones (como agregar B, Ti, Nb, V, etc.), la modificación de tierras raras y el fortalecimiento de compuestos.Estos oligoelementos forman compuestos en el acero, como agregar B y otros oligoelementos para formar boruro en acero, y agregar Ti, Nb, V para formar carburo de alta dureza para mejorar la resistencia al desgaste del acero.WC y AlO se agregan en el proceso de fundición.El compuesto de matriz de acero se forma reforzando la matriz de acero con partículas iguales.
2) materiales cerámicos
Materiales cerámicos.Los materiales utilizados como cerámicas resistentes al desgaste incluyen principalmente cerámicas de óxido, cerámicas de carburo y cerámicas de nitruro.Las cerámicas típicas resistentes al desgaste incluyen alúmina, carburo de silicio, nitruro de silicio, etc. Los materiales cerámicos son muy frágiles.Por lo tanto, el endurecimiento de materiales cerámicos resistentes al desgaste es la principal dirección de investigación.El carburo cementado, también conocido como cermet, es una aleación a base de Co reforzada con partículas de WC o TiC.Este material se usa comúnmente como herramienta, herramienta abrasiva y otras piezas que requieren una resistencia al desgaste muy alta.
3) Materiales poliméricos resistentes al desgaste.
Los materiales poliméricos resistentes al desgaste incluyen principalmente nailon, poliuretano, resina epoxi y caucho.Las desventajas de los materiales poliméricos son la baja dureza y la baja temperatura de servicio.Por lo tanto, el fortalecimiento de partículas o fibras cerámicas comunes puede mejorar su resistencia y resistencia al desgaste.
Las empresas modernas suelen adoptar tecnología de alta velocidad para lograr objetivos económicos.La eficiencia de la planta está determinada por los siguientes parámetros:
•Características y durabilidad del equipo;
•Costo de inversión, costo de operación, costo de mantenimiento y reparación.
Entre ellos, lo más importante es ser seguro y confiable en la producción y reducir el mantenimiento.Por lo tanto, es muy importante reducir el desgaste y la corrosión de los equipos que funcionan a alta velocidad.Con las características sobresalientes de los materiales cerámicos, el uso de productos cerámicos puede resolver los problemas de resistencia al desgaste y resistencia a la corrosión requeridos en muchas aplicaciones.En comparación con los materiales metálicos y los polímeros, la cerámica tiene mejor resistencia al desgaste, resistencia a la corrosión y aislamiento térmico.
Tipos comunes de cerámicas resistentes al desgaste
Cerámica de óxido
1. Cerámica de alúmina
Las cerámicas de alúmina generalmente se refieren a materiales cerámicos α con alúmina como la fase cristalina principal.Según los diferentes contenidos de alúmina, las cerámicas de alúmina se pueden dividir en 75 porcelanas, 85 porcelanas, 90 porcelanas, 95 porcelanas y 99 porcelanas.con α- Los materiales cerámicos con alúmina como fase cristalina principal tienen las siguientes excelentes propiedades:
•Muy alta dureza y resistencia mecánica,
•Buena resistencia a la abrasión, conductividad térmica y fuerza eléctrica.
•Alta resistencia de aislamiento
•Pérdida dieléctrica baja
•El rendimiento eléctrico es relativamente estable con el cambio de temperatura y frecuencia.
•Fabricación conveniente
•La superficie es uniforme y plana;
Las cerámicas de alúmina se han utilizado ampliamente como materiales de aislamiento eléctrico.Hasta ahora, se han encontrado más de diez tipos de estructuras cristalinas de Al2O3, pero hay principalmente tres tipos.A temperaturas superiores a 1300 ℃, otras fases cristalinas se transforman casi por completo en α-Al2O3.
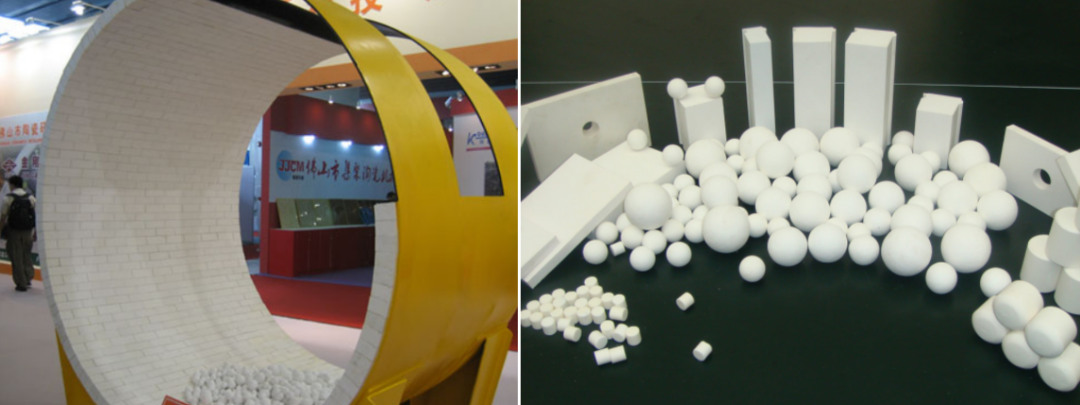
Debido a su amplia fuente, bajo precio y buena resistencia al desgaste, los materiales cerámicos de alúmina son ampliamente utilizados en la industria.Los resultados muestran que la resistencia al desgaste por erosión del material cerámico con un 95 % de Al2O3 es más de 5 veces mayor que la del hierro fundido con alto contenido de cromo (Cr15Mo3).Para la fricción y el desgaste, cuando el contenido de alúmina es bajo, el contenido de alúmina tiene un efecto sobre la resistencia al desgaste de las cerámicas de alúmina.Con el aumento del contenido de Al2O3, aumenta su resistencia al desgaste.El efecto es más significativo en la molienda húmeda.
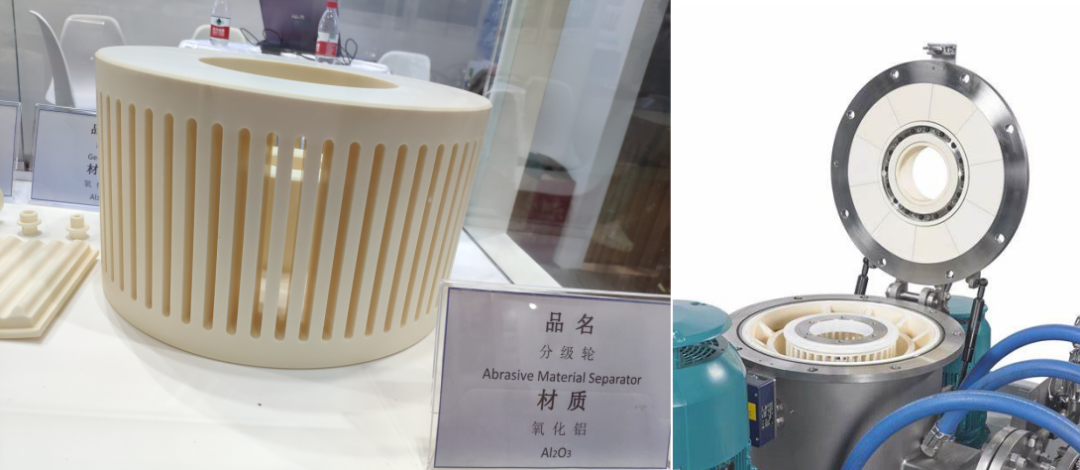
2. Cerámica de circonio
El medio de molienda de zirconio tiene alta densidad, alta resistencia y tenacidad.En realidad, la gravedad específica de la bola de alúmina es de aproximadamente 3,6 g/cm3, mientras que la de la bola de zirconio es de aproximadamente 6,0 g/cm3.Por lo tanto, la zirconia tiene una excelente resistencia al desgaste y una eficiencia de molienda muy alta, y puede prevenir la contaminación del material.Es especialmente adecuado para molienda húmeda y dispersión.En la actualidad, ha sido ampliamente utilizado en cerámica, materiales magnéticos, recubrimientos, tintas, industrias farmacéutica y alimentaria, como pintura automotriz avanzada, pintura para teléfonos móviles, tinta de inyección de tinta, cosméticos avanzados, etc. Con su alta gravedad específica, alta tenacidad y excelente resistencia al desgaste, las bolas de molienda de zirconio se han convertido gradualmente en los medios de molienda más utilizados en el mercado.

En la ingeniería de polvos, la zirconia se puede utilizar como medio de molienda.Al mismo tiempo, la zirconia también se puede utilizar como parte del molino de arena.La tarea del molino de arena es moler.Un excelente molino de arena debe tener las ventajas de una alta eficiencia de molienda, un rendimiento estable del equipo y una alta calidad del producto.Para asegurar estas ventajas, es necesario plantear requisitos para sus accesorios:
•Excelente resistencia al desgaste, es decir, baja tasa de desgaste durante la molienda, lo que no causará una contaminación grave de los productos de molienda;
•La gran dureza, es decir, lo suficientemente grande como para garantizar la alta eficiencia de la molienda.
Entre las piezas de cerámica, la zirconia no solo es la más utilizada, sino también la pieza de cerámica más madura en el molino de arena.Entre los cuatro materiales de diamante (zirconia, alúmina, carburo de silicio y nitruro de silicio) con tecnología madura, la zirconia tiene la mejor tenacidad.En el molino de arena giratorio de alta velocidad, la ventaja de la zirconia como rotor es más obvia.En el proceso de rotación de alta velocidad, el proceso de rectificado por contacto entre el rotor y el material provocará fácilmente grietas en las piezas de cerámica.Las piezas de cerámica se romperán con el tiempo.Solo las cerámicas de zirconio pueden cumplir con la tenacidad de servicio de esta condición de trabajo especial.La aplicación de rotores cerámicos cumple con los requisitos para la preparación y aplicación de muchos polvos ultrafinos de alta pureza sin contaminación ferromagnética.
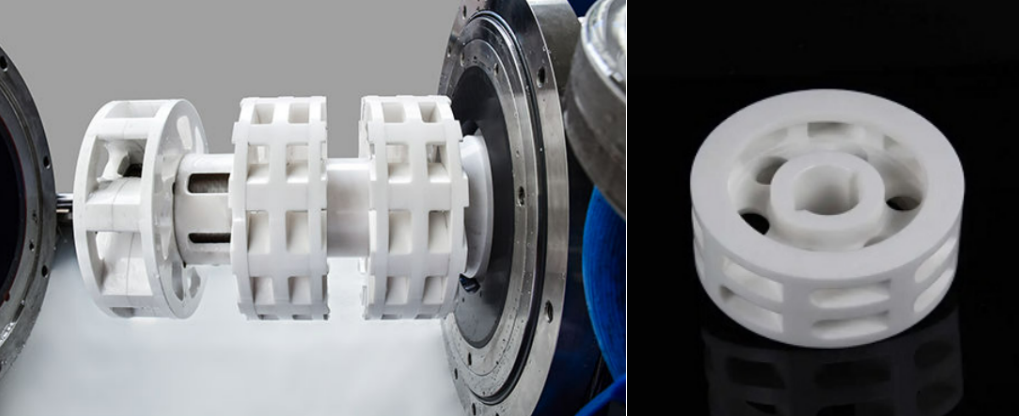
3. Cerámica compuesta de aluminio y alúmina de circonio
Con su alta dureza, propiedades químicas estables y precio adecuado, las bolas de cerámica de alúmina son ampliamente utilizadas.La bola de molienda de zirconio tiene una gran proporción y buena tenacidad.En la actualidad, también se aplica en muchos mercados.En realidad, la fragilidad de las cerámicas de Al2O3 dificulta seriamente la aplicación y el desarrollo de las cerámicas de alúmina.En los últimos años, los investigadores intentan mejorar las propiedades mecánicas de las cerámicas de alúmina añadiendo una segunda fase.
La alúmina tiene una alta dureza, mientras que la zirconia tiene una buena tenacidad.Los dos materiales forman excelentes compuestos con alta resistencia y dureza en el producto de ZTA, que se utilizan más ampliamente.Las cerámicas ZTA tienen una alta resistencia a la flexión y tenacidad a la fractura a temperatura ambiente, así como un excelente rendimiento resistente al desgaste.Este material cerámico compuesto no solo muestra las características de alta tenacidad y alta resistencia de la cerámica de zirconio, sino que también conserva las ventajas de la alta dureza de la cerámica de alúmina.Con la mejora de las propiedades mecánicas integrales, su resistencia al desgaste también se ha mejorado considerablemente.La proporción específica de los dos materiales se puede ajustar de acuerdo con los requisitos de uso reales de los usuarios.Las propiedades de la cerámica de alúmina endurecida con zirconia son mejores que las de la cerámica de alúmina 99, pero sus precios son más bajos que los de la cerámica de zirconia.Los abrasivos cerámicos de aluminio y circonio/revestimientos resistentes al desgaste se modifican y endurecen mediante la introducción de oligoelementos de circonio.El uso del endurecimiento por transformación de fase para formar una estructura policristalina conduce a mejorar la resistencia, la tenacidad y la resistencia al desgaste del producto.Esto también mejora en gran medida la resistencia al impacto de los abrasivos cerámicos/revestimientos resistentes al desgaste.
Cerámica de carburo
Dependiendo de su alta dureza, alta resistencia y alta resistencia al desgaste, las cerámicas de carburo se usan ampliamente en ambientes de alta temperatura con resistencia a la corrosión y resistencia al desgaste.Las cerámicas de alta resistencia al desgaste incluyen carburo de silicio y carburo de boro.
1. Cerámica de carburo de silicio
Debido a sus excelentes propiedades, las cerámicas de carburo de silicio se utilizan ampliamente en defensa nacional, maquinaria, metalurgia, electrónica y otros campos industriales.
Entre muchos materiales cerámicos, el carburo de silicio tiene alta dureza, resistencia a altas temperaturas, buena estabilidad térmica, bajo coeficiente de expansión térmica y excelente conductividad térmica.El carburo de silicio siempre ha sido un tema candente de investigación en la ciencia de los materiales.En comparación con la zirconia, el carburo de silicio utilizado en el cilindro de molienda del molino de arena tiene al menos varias ventajas, como una rápida disipación del calor, un bajo costo y una mayor resistencia al desgaste.La ventaja de la rápida disipación de calor puede prevenir la aglomeración de materiales en el cuerpo de molienda debido a la alta temperatura, mejorando así la eficiencia de molienda.En términos de resistencia al desgaste, el carburo de silicio tiene un rendimiento excelente.Sin embargo, también tiene los inconvenientes de una tenacidad insuficiente y una fácil fragmentación.No es fácil hacer un barril grande.
2. Carburo de boro
El carburo de boro prensado en caliente es un compuesto refractario no metálico.Es una de las sustancias más duras en los abrasivos artificiales.Los productos prensados en caliente tienen una alta resistencia al desgaste.El producto es gris negro y brillante.Las cerámicas de carburo de boro tienen una buena resistencia al desgaste.Tiene importantes aplicaciones en el campo de la resistencia al desgaste.Bajo condiciones severas, la boquilla hecha de cerámica de carburo de boro tiene una larga vida útil.Es mucho más alto que la boquilla hecha de óxido de aluminio, carburo de tungsteno y otros materiales.
En la operación unitaria de la ingeniería de polvos, el polvo cerámico se prepara mediante un secador por aspersión centrífugo.Este método tiene las ventajas de una menor contaminación, una velocidad de secado rápida, un contenido de agua uniforme, una distribución estrecha del tamaño de las partículas, una buena fluidez del polvo, etc. Sin embargo, muchos polvos cerámicos tienen una gran dureza y se desgastan mucho en las boquillas centrífugas giratorias de alta velocidad.Al adoptar material de carburo de boro, es eficaz para mejorar la vida útil de la boquilla.
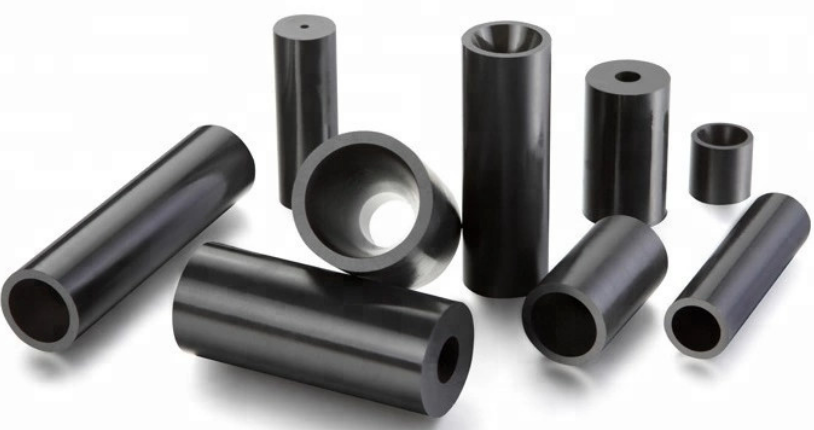
Cerámica de nitruro
1. Cerámica de nitruro de silicio
Las cerámicas de nitruro de silicio tienen una gravedad específica pequeña, un coeficiente de expansión térmica bajo, una buena resistencia al choque térmico y una alta tenacidad a la fractura.Son ampliamente utilizados en la industria aeroespacial, motores de automóviles, maquinaria, industria química y otros campos, especialmente como un nuevo material estructural de alta temperatura.
En el campo de la ingeniería de polvos, la densidad de la rueda clasificadora del molino de chorro de nitruro de silicio es de 3,2 g/m.Su peso corporal es 2/3 del material metálico.La característica de mayor uso de la rueda de clasificación de nitruro de silicio es evitar la contaminación por metales.Además, la gravedad específica es un 40 % menor que la de las cerámicas de zirconio.Esto no solo puede reducir en gran medida el consumo de energía del motor, sino que también requiere menos motor.Bajo el motor existente, se puede realizar el overclocking para obtener partículas más finas.
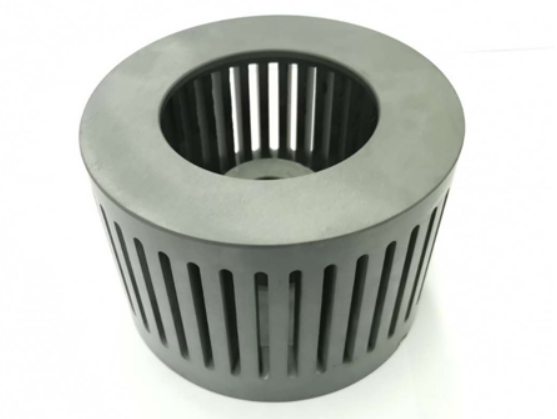
Como un nuevo tipo de medio de molienda, el nitruro de silicio ha ingresado al campo de aplicación industrial.El nitruro de silicio ha atraído mucha atención debido a su índice de desgaste extremadamente bajo y sus excelentes propiedades mecánicas.Aunque limitado por el costo y el nivel de procesamiento del nitruro de silicio, el nitruro de silicio no se usa tan ampliamente.La pequeña gravedad específica del nitruro de silicio no conduce a una molienda eficiente.Sin embargo, el nitruro de silicio sigue siendo un material abrasivo potencial de acuerdo con los requisitos de bajo desgaste del uso de medios de molienda.
2. Nitruro de alúmina
Las cerámicas de nitruro de aluminio tienen propiedades de alta dureza y resistencia a altas temperaturas.Se puede utilizar como herramientas de corte, muelas abrasivas y troqueles de trefilado, así como materias primas para la fabricación de materiales para herramientas y materiales cerámicos metálicos.Las cerámicas de nitruro de aluminio también tienen una excelente resistencia al desgaste.Se puede utilizar como pieza resistente al desgaste.Debido a su alto costo, solo puede usarse para piezas con desgaste severo.Recubrimiento de algunas superficies metálicas o no metálicas fácilmente oxidables con recubrimiento AIN.Esto puede mejorar su resistencia a la oxidación y al desgaste;También se puede utilizar como revestimiento anticorrosivo, como el procesador de sustancias corrosivas y el revestimiento de contenedores.
Hora de publicación: 03-dic-2022