Honeycomb Ceramic Foam Filter
Special foam ceramic filter
Foam ceramic filter is a foam shaped ceramic product that is immersed in the ceramic slurry made of fire-resistant aggregate, sintering aid, binder and other micro powders and water, and after extruding the excess slurry, the remaining ceramic material wrapped around the foam fiber is dried and sintered at high temperature. The carrier of foam ceramic filter is generally polyurethane foam.
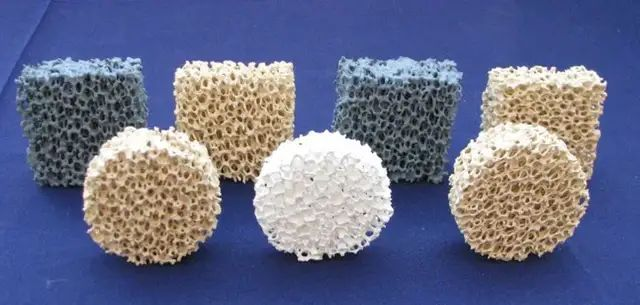
Foam ceramic filter
Foam ceramics have similar pore structure to foam plastics. Its open-cell rate reaches 85% - 90%. The earliest foam ceramic filter was the foam ceramic filter for aluminum alloy which is successfully developed by R.R.Mollard and N.Davison in US company of Consolidated Aluminum in 1978. It is called Selee/Al. Subsequently, Japan, Britain, Germany, Switzerland and other developed countries also developed foam ceramic filters for casting various alloys.
The first foam ceramic filter used for aluminum alloy filtration was developed by Harbin University of technology in China in1982. Later, in the mid-1980s, foam ceramic filters (cff-i type) were developed for ferrous metal filters.
Dongfeng Automobile was the first to produce important castings which should be the sand core screen made of resin sand and hot box. However, they have disadvantages of large eyelet and low high temperature resistance.
In the 1980s, it was replaced by the screen sintered with bauxite and large holes.
In the early 1990s, the filter screen woven with refractory fiber was used. In order to solve the problem of being easily broken by molten iron, a refractory screen is added under the woven screen. Its cost is increased while the process is very cumbersome.
Finally, Dongfeng Automobile tested and used foam ceramic filter, which has been used for more than 30 years. This not only reduced the reject rate of slag inclusion, sand hole and air hole by nearly 70%, but also simplified the gating system, increased the process yield by 10% and reduced the cost by 6%. The corporate and social benefits have been significantly improved.
Due to the different pouring temperatures of the cast alloys, the foam ceramic filters with fire resistance should be selected for the castings. In recent decades, foam ceramic filters of various materials have been developed at home and abroad according to the performance of different alloys.
Liquid metal corresponding to several foam ceramics
Foam ceramic filter material |
Type of metal liquid suitable for filtration |
Application characteristics |
Silicon carbide |
Copper alloy, ductile iron, gray iron, ductile iron |
①Improving the quality of nodular cast iron, gray iron and ductile iron castings;It is helpful to slow down the turbulence degree of molten iron in the runner, and has excellent thermal shock resistance and high temperature strength, which can withstand the extreme environment in the process of cast iron. ② Purifying iron solution; ③ Improving the quality of iron castings; ④ Reducing the number of oxides in cast iron; ⑤ Stable filling time; |
Alumina |
Aluminum and aluminum alloy |
① Improve the quality of aluminum alloy and other non-ferrous alloy castings; ② Improve the metallographic structure; ③ Improve the mechanical properties; ④Rectifier action; |
Zirconia |
Carbon steel, alloy steel, stainless steel |
①Applied for purification of carbon steel, alloy steel and stainless steel solutions; It can withstanding certain technical requirements; it can filter the materials with slag inclusion and corroded model; it can slow down turbulence, thus reducing re oxidation slag inclusion; ② Purifying steel casting solution; ③ Improving the yield of steel castings ④ Reducing inclusions in steel castings ⑤ Reducing internal reoxidation defects ⑥ Reducing subsurface defects after machining; |
Magnesium oxide |
Magnesium alloy |
① Magnesium alloys are more active than other non-ferrous metals; The free energy of magnesium oxide formation is very low; The molten magnesium alloy liquid at high temperature can easily react with the main components of ceramic filter to make filter dissolve rapidly. ② Purifying magnesium alloy solution ③ Improving internal quality of magnesium alloy; |
Nowadays, the application of foam ceramic filter in the field of liquid casting alloy filtration has made great progress, which have been expanded to metallurgy.
For example, Hi-Tech Ceramic Company in US used its high-purity partially stabilized foam ceramic filter to filter large superalloy steel ingots weighing up to 22 tons. The pouring time is as long as 60min.
By placing high-purity partially stable foam ceramic filters on the partition wall of the continuous casting tundish with a capacity of 15 tons, Nippon Steel of Japan has improved the purification degree of its corrosion-resistant steel blanks by about 16%. The distribution of inclusions smaller than 6μm is also improved.
In China, foam ceramic filters are also gradually widely used in the casting of liquid alloys. With the further development of modern casting technology, the requirements for casting quality will be higher and higher. The performance of foam ceramic filter will be further developed and broken through in the process of production practice, which has wide development prospects and other possibilities.
Item |
Cordierite |
Mullite cordierite |
Mullite |
Corundum mullite |
Zirconium mullite |
Aluminum content % |
35-37 |
40-50 |
50-60 |
68-73 |
68-73 |
Type of hole |
Square hole Circular hole |
Square hole Circular hole |
Square hole Circular hole |
Square hole Circular hole |
Square hole Circular hole |
Number of holes CPSI |
60-400 |
60-400 |
60-400 |
60-400 |
60-400 |
Micropore μm |
2~3 |
2~3 |
2~3 |
2~3 |
2~3 |
Thermal expansion coefficient 10-6/K |
≤1.8 |
≤3 |
≤5 |
≤5.5 |
≤5 |
Softening temperature ℃ |
1380 |
1500 |
1550 |
1700 |
1700 |
Normal temperature compressive strength MPa |
≥12 |
≥15 |
≥15 |
≥15 |
≥15 |
Application |
Aluminum alloy casting |
Ductile iron and gray cast iron casting |
Stainless steel casting |
Mullite honeycomb ceramic filter
Mullite honeycomb ceramic filter has been widely used for filtering molten metal in metallurgy and casting industries. It uses mullite or cordierite ceramic materials. Its high quality and high density straight mesh makes the product have the characteristics of high heat shock resistance and high sintering temperature resistance. In addition, it has a natural chemical adsorption (affinity) capacity for oxides. The inner wall of the hole adsorbs impurities (including particles smaller than the size of the hole) in the metal liquid, thereby improving the filtering effect.
The advanced extrusion production process makes the ceramic filter have a unique square and triangular design. It increases the contact area with ceramics, and improves the ability of the filter to absorb and capture small impurities. Compared with the non extrusion filter, the metal liquid flows smoothly. It is important to improve the pouring speed and continuity, as well as mechanical properties of the casting. It is also positive to reduce the casting scrap rate and extend the service life.
Foam ceramic metal solution filter
Foam ceramic filter is a kind of special ceramic product. It has a foam like porous structure. It has many advantages, such as stable chemical properties, high strength, high temperature resistance, good thermal shock resistance, large specific surface area, etc. Foam ceramic filter has been widely used in metallurgy, casting, environmental protection and other fields.