耐摩耗材料分野における先端セラミックスの応用
耐摩耗性および耐腐食性産業は、表面処理産業の一分野です。これは、電力、鉄鋼、化学鉱業、セメントおよびその他の産業における機器およびワークピースの摩耗および腐食の問題を解決するための、予防的ケアおよび再生技術サービスの新興産業です。耐摩耗性と耐腐食性産業は活力が強いです。産業機器の摩耗と腐食から保護することで、その耐用年数を大幅に改善し、メンテナンスや交換による鋼材やその他の材料の消費を減らして資源を節約できます。耐摩耗性および耐腐食性産業は、資源を節約し、環境を保護し、循環経済を促進するための重要な手段です。また、企業が省エネルギー、排出量とコストの削減、および経済効率の向上を達成するための強力なアシスタントでもあります。耐摩耗性および耐腐食性産業には、横断的、限界的、および学際的な特徴があります。
耐摩耗性および耐腐食性産業の中核は、関連産業における新しい材料と技術の適用です。主に、耐摩耗セラミック技術、溶射、表面仕上げおよび耐摩耗プレート、レーザークラッディング、耐腐食および耐摩耗コーティング技術、耐腐食技術、耐摩耗材料技術などが含まれます。
先端セラミックスの耐摩耗材料分野への応用
統計によると、摩擦は世界の可処分エネルギーの約 1/3 を消費し、機械部品の約 80% は摩耗によって故障します。機械部品の摩耗故障は、摩擦材の選択と使用条件に密接に関係しています。一般に、摩耗量の少ない摩擦摩耗条件下で使用される材料を耐摩耗材料と呼びます。摩擦係数が小さい材料は減摩材料と呼ばれます。摩擦係数の大きい材料を摩擦材と呼びます。さまざまな作業条件と、機械部品に必要な摩擦および摩耗特性に適した材料を正しく選択して使用することが非常に重要です。例えば、高衝撃環境では耐摩耗材料として高マンガン鋼を選択するのが一般的に適切ですが、衝撃荷重が小さい環境では、高マンガン鋼は高マンガン鋼の変形硬化の利点を発揮できません。より適切な。さらに、減摩材料と摩擦材料の両方が同時に優れた耐摩耗性を備えていることが望まれます。材料の優れた耐摩耗性は、機械部品の耐用年数を延ばすだけでなく、部品の交換と労働者の労働強度を減らすだけでなく、エネルギーと材料資源を節約することもできます。したがって、さまざまな作業条件と機械部品の性能要件に応じて、機械設備の性能を向上させ、エネルギーを節約する上で、耐摩耗性材料を正しく選択することは非常に重要です。
耐摩耗材料にはどのような種類がありますか?
耐摩耗材料には多くの種類があり、化学組成に応じて、金属耐摩耗材料、セラミック耐摩耗材料、ポリマー耐摩耗材料、耐摩耗複合材料に分類できます。材料構造によると、一体型耐摩耗材料と表面耐摩耗材料に分けることができます。耐摩耗材料は、さまざまな使用温度に応じて、常温耐摩耗材料と高温耐摩耗材料に分けることができます。
①金属素材。金属材料は、耐摩耗鋼と耐摩耗鋳鉄にも分けられます。一般的に使用されるのは、耐摩耗合金鋼、高マンガン鋼、軸受鋼、工具鋼です。変形硬化により耐摩耗性を向上させる高マンガン鋼を除いて、他の耐摩耗鋼は、主に炭化物形成元素を添加し、炭素と炭化物を形成することにより、鋼の硬度と耐摩耗性を向上させます。現在、耐摩耗鋼の開発動向は、マイクロアロイ(B、Ti、Nb、Vなどの添加など)強化、希土類改質、複合強化です。これらの微量元素は、鋼中に B などの微量元素を添加してホウ化物を形成したり、Ti、Nb、V などを添加して高硬度炭化物を形成して鋼の耐摩耗性を向上させるなど、鋼中で化合物を形成します。WC と AlO は、鋳造プロセスで追加されます。鋼マトリックス複合材は、鋼マトリックスを等粒子で強化することによって形成されます。
②セラミック素材。耐摩耗セラミックスとして使用される材料には、主に酸化物セラミックス、炭化物セラミックス、窒化物セラミックスがあります。典型的な耐摩耗性セラミックには、アルミナ、炭化ケイ素、窒化ケイ素などがあります。セラミック材料は非常に脆いため、耐摩耗性セラミック材料の強化が主な研究方向です。サーメットとも呼ばれる超硬合金は、WC または TiC 粒子で強化された Co ベースの合金で、工具、研磨材、および非常に高い耐摩耗性を必要とするその他の部品として一般的に使用されています。
③ポリマー耐摩耗材料。ポリマーの耐摩耗性材料には、主にナイロン、ポリウレタン、エポキシ樹脂、ゴムが含まれます。ポリマー材料の欠点は、硬度が低く、使用温度が低いことです。そのため、強度と耐摩耗性を向上させるためにセラミック粒子または繊維を使用して強化することがよくあります。
経済的な目的のために、現代の企業は通常、高速テクノロジーを採用しています。工場の効率は、次のパラメーターによって決まります。機器の特性と耐久性。投資コスト、運用コスト、保守および修理コストのうち、最も重要なのは生産における安全性と信頼性、および保守の削減です。したがって、高速走行装置の摩耗と腐食を減らすことは非常に重要です。セラミックス材料の優れた特性により、セラミックスを使用することで、多くの用途で要求される耐摩耗性と耐食性の問題を解決できます。金属材料やポリマーと比較して、セラミックスは耐摩耗性、耐食性、断熱性に優れています。
一般的なタイプの耐摩耗性セラミックス?
酸化物セラミックス
1. アルミナセラミックス
アルミナセラミックスは通常、アルミナを主な結晶相とするα-セラミックス材料を指します。異なるアルミナ含有量によると、75磁器、85磁器、90磁器、95磁器、99磁器があります。α- 酸化アルミニウムを主結晶相とするセラミックス材料は、高い硬度と機械的強度、優れた耐摩耗性、熱伝導性、高い電気的強度と絶縁抵抗、低い誘電損失、温度と周波数の変化に対する安定した電気的性能を備え、広く使用されています。便利な製造、均一で平らな表面のため、電気絶縁材料として使用されます。これまでに10種類以上のAl2O3結晶構造が発見されていますが、主に3種類です。1300 ℃以上の温度では、他の結晶相はほぼ完全に α-Al2O3 に変換されます。
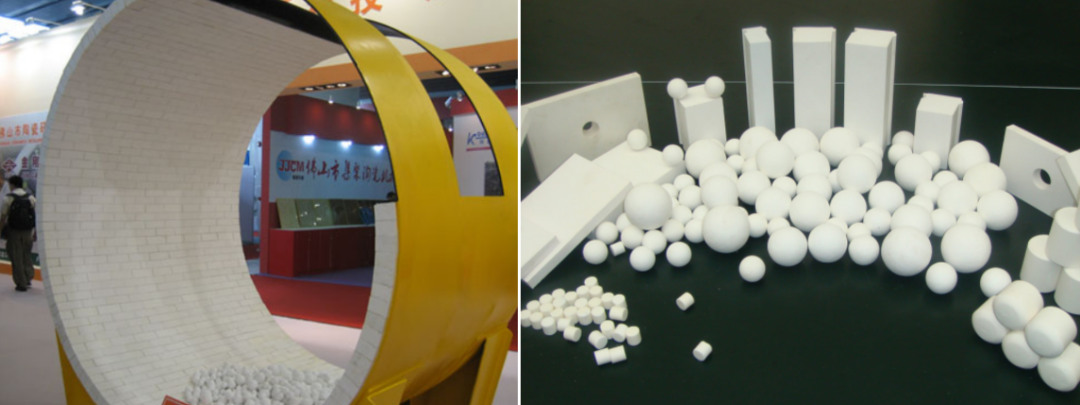
アルミナセラミック材料は、豊富な供給源、低価格、優れた耐摩耗性により、産業界で広く使用されています。結果は、95% Al2O3 セラミック材料のエロージョン摩耗抵抗が、高クロム鋳鉄 (Cr15Mo3) の 5 倍以上であることを示しています。摩擦と摩耗については、アルミナ含有量が低い場合、アルミナ含有量はアルミナセラミックスの耐摩耗性に影響を与えます。Al2O3含有量の増加に伴い、耐摩耗性が向上し、その効果は湿式研削でより顕著になります。
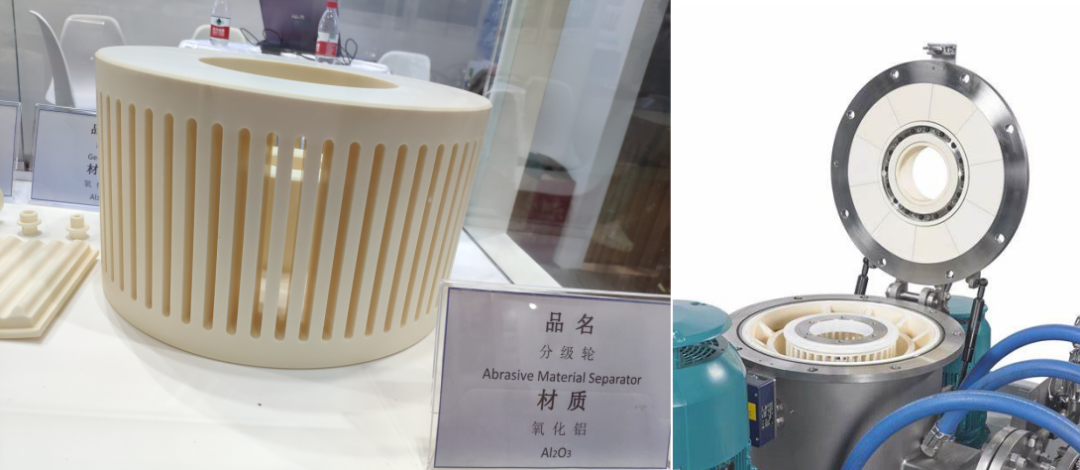
2. ジルコニアセラミックス
ジルコニア粉砕媒体は、高密度(アルミナボールの比重は約3.6g/cm3、ジルコニアボールの比重は約6.0g/cm3)で、強度と靭性が高いため、耐摩耗性に優れ、非常に高い研削力を持っています。効率、および物質的な汚染を防ぐことができます。特に湿式粉砕・分散に適しています。現在、セラミックス、磁性材料、コーティング、インク、医薬品、食品産業で広く使用されています。たとえば、高度な自動車塗料、携帯電話の塗料、インクジェット インク、高度な化粧品などです。ジルコニア研磨ビーズは、比重が高いため、市場で最も広く使用されている研磨媒体になっています (アルミナ ボールの比重は約3.6g/cm3、ジルコニアボールの比重は約6.0g/cm3)で、靭性が高く、耐摩耗性に優れています。

粉末工学では、ジルコニアは粉砕媒体として使用されるほか、サンドミルの付属品としても使用されます。誰もがサンドミルに精通しています。その仕事は研削です。優れたサンドミルには、高い粉砕効率、安定した設備性能、高い製品品質という利点が必要です。これらの利点を確保するために、付属品の要件を提示する必要があります。まず、耐摩耗性があります。つまり、研削時の摩耗率が低く、研削製品に深刻な汚染を引き起こしません。2、硬度が高いため、高い研削効率を確保できます。ジルコニアは、セラミック部品の中でもサンドミルに使用される最も成熟したセラミック部品であり、幅広い用途があります。最も成熟した 4 つのダイヤモンド素材、ジルコニア、アルミナ、炭化ケイ素、窒化ケイ素の中で、ジルコニアは最高の靭性を備えています。高速回転サンドミルでは、ローターとしてより明白な利点があります。高速回転のプロセスでは、ローターと材料の間の接触研削プロセスにより、セラミック部品に亀裂が生じやすくなり、時間の経過とともにセラミック部品が破損する可能性があります。ジルコニアセラミックスだけが、この特殊な作業条件の使用タフネスを満たすことができます。セラミックローターの適用は、強磁性汚染のない多くの高純度超微粉末の調製と適用の要件を満たしています。
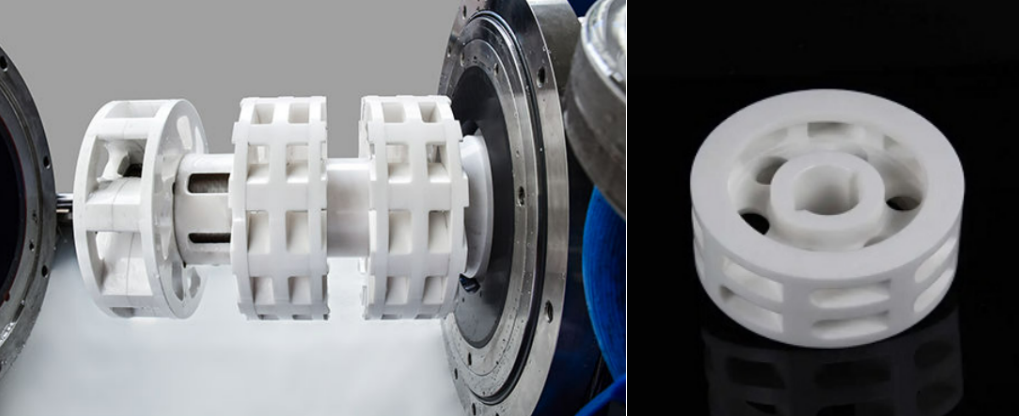
3. ジルコニア・アルミナ・アルミ複合セラミックス
アルミナ セラミック ボールは、硬度が高く、化学的性質が安定しており、適切な価格であるため、広く使用されています。ジルコニア研削ボールは、比率が大きく、靭性が高いため、多くの市場でも使用されています。しかし、Al2O3 セラミックスのもろさは、アルミナ セラミックスの応用と開発を深刻に妨げています。近年、研究者は、第 2 相を追加することにより、アルミナ セラミックスの機械的特性を改善しようと試みてきました。
酸化アルミニウムは硬度が高く、ジルコニアは靭性に優れています。2 つの材料は、より広く使用されている高強度と高靭性を備えた優れた複合材料を形成します。ZTA セラミックスは室温で高い曲げ強度と破壊靭性を備えているため、ジルコニア強化セラミックスは優れた耐摩耗性を備えています。この複合セラミックス材料は、高い靭性と強度を持つジルコニアセラミックスの特性を示すだけでなく、高硬度のアルミナセラミックスの利点も保持しています。この総合的な機械的特性の向上により、耐摩耗性も大幅に向上しました。2つの材料の特定の比率は、ユーザーの実際の使用要件に従って調整できます。ジルコニア強化アルミナ セラミックスの特性は 99 アルミナ セラミックスよりも優れており、価格はジルコニア セラミックスよりも低くなっています。ジルコニウム アルミニウム セラミック研磨材/耐摩耗性ライニングは、微量元素ジルコニウムを導入することで改質および強化され、相変態によって強化され、多結晶構造を形成します。強度と靭性が向上し、耐摩耗性が良好なため、セラミック研磨材/耐摩耗性ライニングの衝撃靭性が大幅に向上します。
超硬セラミックス
超硬セラミックスは、硬度が高く、強度が高く、耐摩耗性に優れているため、耐食性と耐摩耗性を備えた高温環境で広く使用されています。炭化ケイ素や炭化ホウ素などの高耐摩耗性セラミックスが一般的です。
1. 炭化ケイ素セラミックス
炭化ケイ素セラミックスは、その優れた特性により、国防、機械、冶金、電子およびその他の産業分野で広く使用されています。多くのセラミック材料の中で、炭化ケイ素は、その硬度が高く、耐熱性が高く、熱安定性が高く、熱膨張係数が低く、熱伝導率が優れているため、材料科学研究のホットスポットとなっています。ジルコニアと比較して、炭化ケイ素は、サンドミルの粉砕シリンダーに適用した場合、熱放散が速い、低コスト、耐摩耗性が高いなど、少なくともいくつかの利点があります。熱放散が速いという利点により、高温による粉砕体内の材料の凝集を防ぐことができ、粉砕効率が向上します。耐摩耗性の面では、炭化ケイ素は優れた性能を発揮しますが、靭性が不十分で、破砕しやすいという欠点もあります。大きなバレルを作るのは簡単ではありません。
2.炭化ホウ素
非金属耐火性化合物であるホットプレス炭化ホウ素は、人工研磨剤の中で最も硬い物質の 1 つです。ホットプレス製品は耐摩耗性が高く、灰黒色で光沢があります。炭化ホウ素セラミックスは耐摩耗性に優れているため、耐摩耗性の分野で重要な用途があります。炭化ホウ素セラミックス製のノズルは、過酷な条件下でも長寿命であり、酸化アルミニウムや炭化タングステンなどの材料に比べてはるかに長寿命です。
粉末工学の単位操作では、遠心噴霧乾燥機を使用してセラミック粉末を調製します。これには、汚染が少なく、乾燥速度が速く、水分含有量が均一で、粒度分布が狭く、粉末流動性が良好であるなどの利点がありますが、多くのセラミック粉体は硬度が高く、高速回転する遠心ノズルに深刻な摩耗を引き起こします。炭化ホウ素を使用すると、ノズルの寿命を効果的に改善できます。
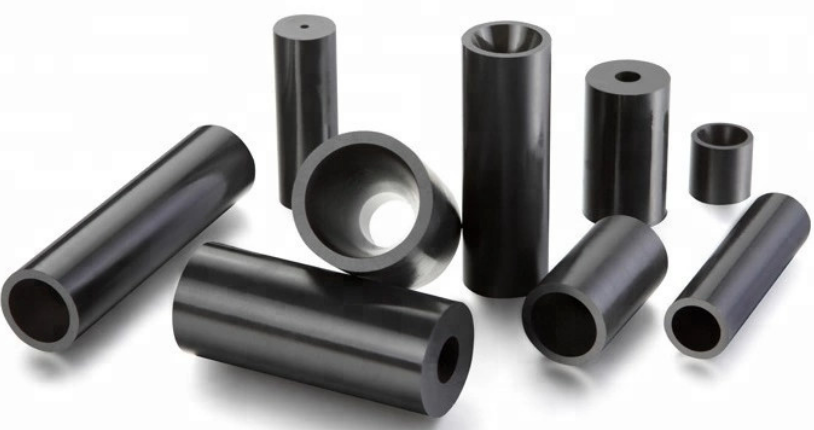
窒化物セラミックス
1. 窒化ケイ素セラミックス
窒化ケイ素セラミックスは、比重が小さく、熱膨張係数が低く、耐熱衝撃性に優れ、破壊靭性が高いです。それらは、航空宇宙、自動車エンジン、機械、化学産業、およびその他の分野で広く使用されており、特に新しい高温構造材料として、明らかな利点があります。
粉体工学の分野では、窒化ケイ素ジェットミルのグレーディングホイールの密度は3.2g/mで、その重量は金属材料の2/3です。窒化ケイ素グレーディングホイールの最大の特長は、金属汚染を防ぐことです。さらに、その割合はジルコニア セラミックスよりも 40% 小さく、モーターのエネルギー消費を大幅に削減できるだけでなく、モーターの要件も少なくなります。既存のモーターの下で、より細かい粒子サイズの粒子を得るために、周波数を超えて達成できます。
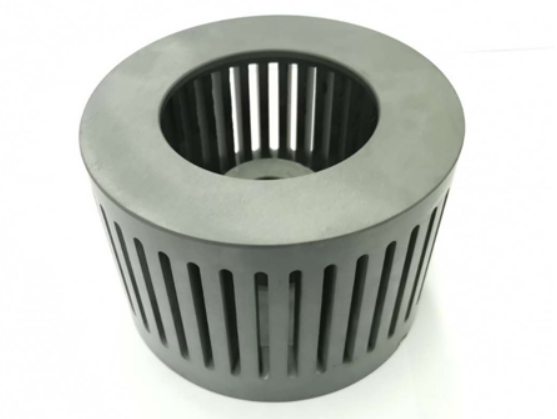
新しいタイプの粉砕媒体としての窒化ケイ素は、産業応用分野に参入しました。摩耗率が極めて低く、機械的特性に優れていることから注目を集めています。窒化ケイ素のコストと処理レベルによって制限されますが、窒化ケイ素はそれほど広く使用されておらず、窒化ケイ素の割合が比較的少ないため、効率的な研削には役立ちませんが、研削媒体の使用には低摩耗が必要です。窒化ケイ素も研磨剤の可能性があります。
2. 窒化アルミニウム
高い硬度と高温強度を備えた窒化アルミニウムセラミックスは、切削工具、砥石、伸線ダイス、および工具材料と金属セラミック材料の原料として使用できます。耐摩耗性にも優れており、耐摩耗部品としてもご使用いただけます。ただし、コストが高いため、摩耗の激しい部品にしか使用できません。酸化しやすい金属または非金属の表面を AIN コーティングでコーティングすると、耐酸化性と耐摩耗性が向上します。また、腐食性物質の処理装置や容器の内張りなどの防食コーティングとしても使用できます。