Applications of Advanced Ceramics in the Field of Wear resistant Materials
Wear and corrosion resistance industry is a branch of surface treatment industry. As emerging industries of preventive care and remanufacturing technology services, they are very important for solving the wear and corrosion problems of equipment and workpieces in power, steel, chemical mining, cement and other industries. The abrasion and corrosion resistant industry has strong vitality. The service life of industrial equipment can be greatly improved through wear and corrosion protection. At the same time, the consumption of steel and other materials caused by maintenance or replacement can be reduced to save resources. Wear and corrosion resistant industry is an important measure to save resources, protect the environment and promote circular economy. They are also powerful assistants for enterprises to achieve energy conservation and emission reduction, reduce costs and improve economic efficiency.
The core of wear and corrosion resistance industry is the application of new materials and technologies in related industries. It mainly includes wear-resistant ceramic technology, thermal spraying, surfacing and wear-resistant plate, laser cladding, anti-corrosion and wear-resistant coating technology, anti-corrosion technology, wear-resistant material technology, etc.
Applications of Advanced Ceramics in the Field of Wear resistant Materials
Based on the statistics, friction consumes about 1/3 of the primary energy in the world. Meanwhile, there are about 80% of machine parts fail due to wear. The wear failure of mechanical parts is closely related to the selection of friction pair materials and service conditions. In general,
►The wear-resistant materials refer to the materials used under friction and wear conditions with small wear amount.
►The antifriction materials refer to the material with small friction coefficient.
►The friction materials refer to the material with large friction coefficient.
It is very important to select and use the right materials correctly based on different working conditions and friction and wear performance required by mechanical parts. For example, the wear-resistant materials used in high impact environments are generally high manganese steel. However, in the environment of small impact load, the use of high manganese steel will not give play to the advantages of deformation hardening of high manganese steel, while the use of high chromium cast iron is more appropriate. No matter antifriction materials or friction materials, both of them should have good wear resistance at the same time. The good wear resistance of materials can not only prolong the service life of mechanical parts, but also reduce the replacement of parts and labor intensity of workers. Especially, the good wear resistance of materials can also save energy and material resources. therefore, it is significant to correctly select wear-resistant materials in improving mechanical equipment performance and saving energy based on different working conditions and mechanical parts performance requirements.
Types of wear-resistant materials
There are various wear-resistant materials in the world.
• Based on their chemical compositions, the wear-resistant materials can be divided into metal wear-resistant materials, ceramic wear-resistant materials, polymer wear-resistant materials and wear-resistant composites.
• Based on different material structures, the wear-resistant materials can be divided into integral wear-resistant materials and surface wear-resistant materials.
• Based on the different using temperature, the wear-resistant materials can be divided into normal temperature wear-resistant materials and high temperature wear-resistant materials.
1) Metallic materials
Metal materials can be divided into wear-resistant steel and wear-resistant cast iron. The commonly used metal materials in production are wear-resistant alloy steel, high manganese steel, bearing steel and tool steel. The wear resistance of high manganese steel is improved by deformation hardening. In addition, other wear-resistant steels mainly improve the hardness and wear resistance of steel by adding carbide forming elements and forming carbides with carbon. At present, the development trend of wear-resistant steel is microalloying (such as adding B, Ti, Nb, V, etc.) strengthening, rare earth modification and composite strengthening. These trace elements form compounds in steel, such as adding B and other trace elements to form boride in steel, and adding Ti, Nb, V to form high hardness carbide to improve the wear resistance of steel. WC and AlO are added in the casting process. The steel matrix composite is formed by strengthening the steel matrix with equal particles.
2)Ceramic materials
Ceramic materials. The materials used as wear-resistant ceramics mainly include oxide ceramics, carbide ceramics and nitride ceramics. Typical wear-resistant ceramics include alumina, silicon carbide, silicon nitride, etc. Ceramic materials are very brittle. Therefore, the toughening of wear-resistant ceramic materials is the main research direction. Cemented carbide, also known as cermet, is a Co based alloy reinforced by WC or TiC particles. This material is commonly used as tool, abrasive tool and other parts requiring very high wear resistance.
3) Polymer wear-resistant materials
The polymer wear-resistant materials mainly include nylon, polyurethane, epoxy resin and rubber. The disadvantages of polymer materials are low hardness and low service temperature. Therefore, strengthening common ceramic particles or fibers can improve their strength and wear resistance.
Modern enterprises usually adopt high-speed technology to achieve economic goals. The efficiency of the plant is determined by the following parameters:
• Equipment characteristics and durability;
• Investment cost, operation cost, maintenance and repair cost.
Among them, the most important thing is to be safe and reliable in production and reduce maintenance. Therefore, it is very important to reduce the wear and corrosion of high-speed running equipment. With the outstanding characteristics of ceramic materials, the use of ceramic products can solve the problems of wear resistance and corrosion resistance required in many applications. Compared with metal materials and polymers, ceramics have better wear resistance, corrosion resistance and thermal insulation.
Common types of wear-resistant ceramics
Oxide ceramics
1. Alumina ceramics
Alumina ceramics usually refer to α- Ceramic materials with alumina as the main crystalline phase. According to the different alumina content, alumina ceramics can be divided into 75 porcelain, 85 porcelain, 90 porcelain, 95 porcelain and 99 porcelain. with α- Ceramic materials with alumina as the main crystalline phase have the following excellent properties:
• Very high hardness and mechanical strength,
• Good abrasion resistance, thermal conductivity and electrical strength
• High insulation resistance
• Low dielectric loss
• The electrical performance is relatively stable with the change of temperature and frequency
• Convenient manufacturing
• The surface is even and flat;
Alumina ceramics have been widely used as electrical insulating materials. Up to now, more than ten kinds of Al2O3 crystal structures have been found, but there are mainly three kinds. At temperatures above 1300 ℃, other crystalline phases are almost completely transformed into α- Al2O3.
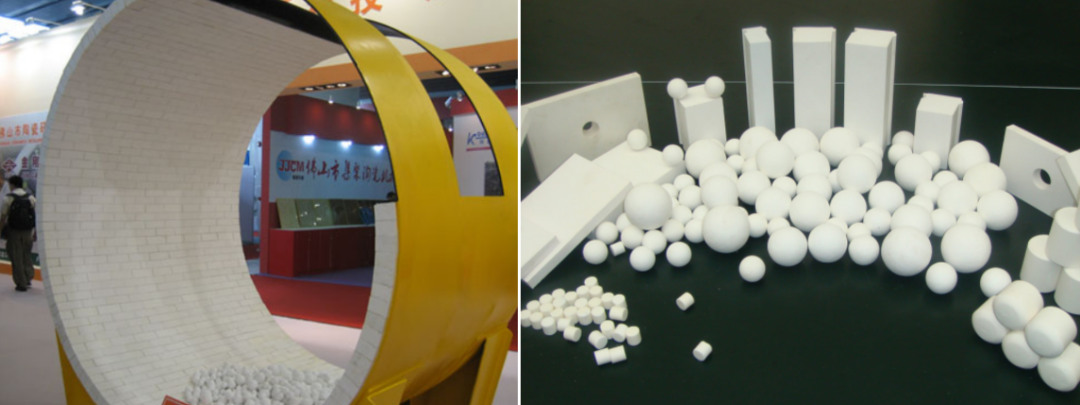
Due to its wide source, low price and good wear resistance, alumina ceramic materials are widely used in industry. The results show that the erosion wear resistance of 95% Al2O3 ceramic material is more than 5 times that of high chromium cast iron (Cr15Mo3). For friction and wear, when the alumina content is low, the alumina content has an effect on the wear resistance of alumina ceramics. With the increase of Al2O3 content, its wear resistance increases. The effect is more significant in wet grinding.
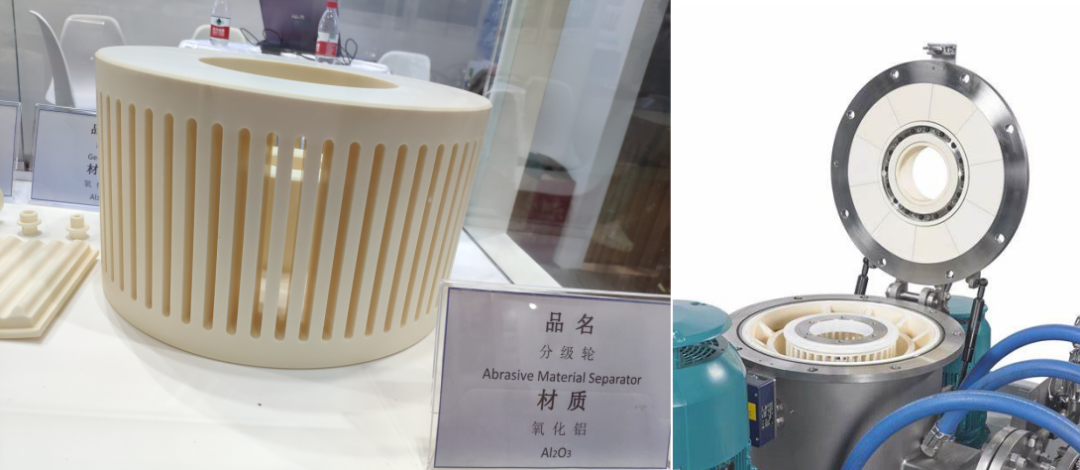
2. Zirconia ceramics
Zirconia grinding medium has high density, high strength and toughness. Actually, the specific gravity of alumina ball is about 3.6g/cm3, while that of zirconia ball is about 6.0g/cm3. Therefore, zirconia has excellent wear resistance and very high grinding efficiency, and can prevent material pollution. It is especially suitable for wet grinding and dispersion. At present, it has been widely used in ceramics, magnetic materials, coatings, inks, pharmaceutical and food industries, such as advanced automotive paint, mobile phone paint, ink-jet ink, advanced cosmetics, etc. With its high specific gravity, high toughness, and excellent wear resistance, zirconia grinding beads have gradually become the most widely used grinding media on the market.

In powder engineering, zirconia can be used as grinding medium. At the same time, zirconia can also be used as a part of the sand mill. The task of the sand mill is to grind. An excellent sand mill needs to have the advantages of high grinding efficiency, stable equipment performance and high product quality. In order to ensure these advantages, it is necessary to put forward requirements for its accessories:
•Excellent wear resistance, that is, low wear rate during grinding, which will not cause serious pollution to the grinding products;
•The large hardness, that is, large enough to ensure the high efficiency of grinding.
Among the ceramic parts, zirconia is not only the most widely used, but also the most mature ceramic part in the sand mill. Among the four diamond materials (zirconia, alumina, silicon carbide and silicon nitride) with mature technology, zirconia has the best toughness. In the high-speed rotating sand mill, the advantage of zirconia as the rotor is more obvious. In the process of high-speed rotation, the contact grinding process between rotor and material will easily lead to cracks in ceramic parts. The ceramic parts will break over time. Only zirconia ceramics can meet the service toughness of this special working condition. The application of ceramic rotors meets the requirements for the preparation and application of many high-purity ultrafine powders without ferromagnetic pollution.
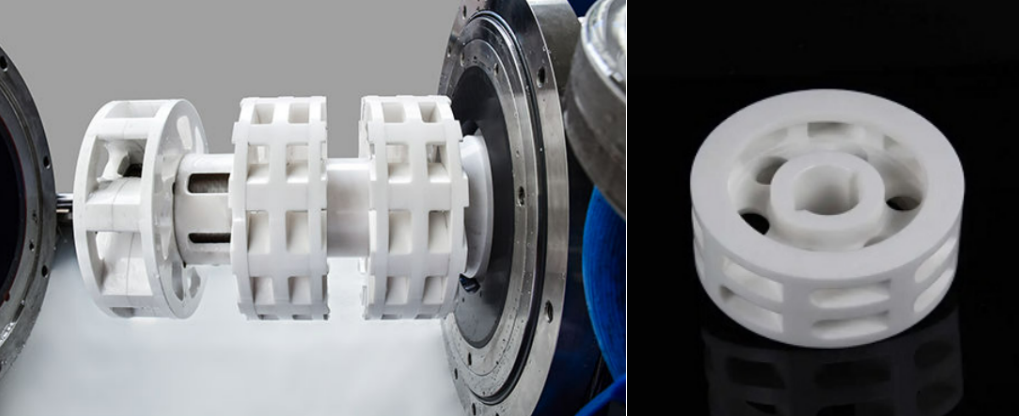
3. Zirconia alumina aluminum composite ceramics
With its high hardness, stable chemical properties and suitable price, alumina ceramic balls are widely used. The zirconia grinding ball has a large proportion and good toughness. At present, it is also applied in many markets. Actually, the brittleness of Al2O3 ceramics seriously hinders the application and development of alumina ceramics. In recent years, researchers try to improve the mechanical properties of alumina ceramics by adding second phase.
Alumina has high hardness, while zirconia has good toughness. The two materials form excellent composites with high strength and high toughness in the product of ZTA, which are more widely used. ZTA ceramics have high bending strength and fracture toughness at room temperature, as well as excellent wear-resistant performance. This composite ceramic material not only shows the characteristics of high toughness and high strength of zirconia ceramics, but also retains the advantages of high hardness of alumina ceramics. With the improvement of the comprehensive mechanical properties, its wear resistance has also been greatly improved. The specific proportion of the two materials can be adjusted according to the actual use requirements of users. The properties of zirconia toughened alumina ceramics are better than 99 alumina ceramics, but their prices are lower than zirconia ceramics. Zirconium aluminum ceramic abrasives/wear-resistant linings are modified and toughened by introducing trace element zirconium. The use of phase transformation toughening to form a polycrystalline structure is conducive to improving the strength, toughness, and wear resistance of the product. This also greatly improves the impact toughness of ceramic abrasives/wear-resistant linings.
Carbide ceramics
Depending on their high hardness, high strength and high wear resistance, carbide ceramics are widely used in high temperature environment with corrosion resistance and wear resistance. High wear resistance ceramics include silicon carbide and boron carbide.
1. Silicon carbide ceramics
Due to their excellent properties, Silicon carbide ceramics are widely used in national defense, machinery, metallurgy, electronics and other industrial fields.
Among many ceramic materials, silicon carbide has high hardness, high temperature resistance, good thermal stability, low coefficient of thermal expansion and excellent thermal conductivity. Silicon carbide has always been a hot research topic in materials science. Compared with zirconia, silicon carbide used in the grinding cylinder of the sand mill has at least several advantages, such as fast heat dissipation, low cost, and more wear resistance. The advantage of fast heat dissipation can prevent the agglomeration of materials in the grinding body due to high temperature, thus improving the grinding efficiency. In terms of wear resistance, silicon carbide has excellent performance. However, it also has the shortcomings of insufficient toughness and easy fragmentation. It is not easy to make a big barrel.
2. Boron carbide
Hot pressed boron carbide is a non-metallic refractory compound. It is one of the hardest substances in artificial abrasives. Hot pressed products have high wear resistance. The product is grey black and glossy. Boron carbide ceramics have good wear resistance. It has important applications in the field of wear resistance. Under severe conditions, the nozzle made of boron carbide ceramics has a long service life. It is much higher than the nozzle made of aluminum oxide, tungsten carbide and other materials.
In the unit operation of powder engineering, ceramic powder is prepared by centrifugal spray dryer. This method has the advantages of less pollution, fast drying speed, uniform water content, narrow particle size distribution, good powder fluidity, etc. However, many ceramic powders have high hardness and are seriously worn to high-speed rotating centrifugal nozzles. By adotping boron carbide material, it is effective to improve the service life of the nozzle.
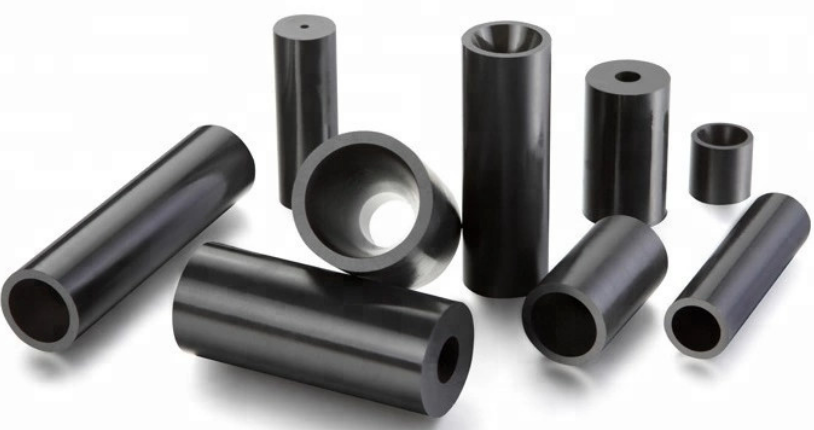
Nitride ceramics
1. Silicon nitride ceramics
Silicon nitride ceramics have small specific gravity, low thermal expansion coefficient, good thermal shock resistance and high fracture toughness. They are widely used in aerospace, automobile engine, machinery, chemical industry and other fields, especially as a new high-temperature structural material.
In the field of powder engineering, the density of the grading wheel of silicon nitride jet mill is 3.2g/m. Its body weight is 2/3 of the metal material. The biggest use feature of silicon nitride grading wheel is to prevent metal pollution. In addition, the specific gravity is 40% smaller than that of zirconia ceramics. This not only can greatly reduce the motor energy consumption, but also requires less motor. Under the existing motor, the overclocking can be realized to obtain finer particles.
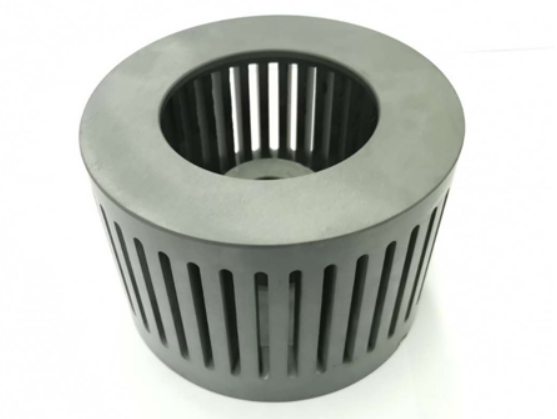
As a new type of grinding medium, silicon nitride has entered the industrial application field. Silicon nitride has attracted much attention due to its extremely low wear rate and excellent mechanical properties. Although limited by the cost and processing level of silicon nitride, silicon nitride is not so widely used. Small specific gravity of silicon nitride is not conducive to efficient grinding. However, silicon nitride is still a potential abrasive material according to the low wear requirements of the use of grinding media.
2. Alumina nitride
Aluminum nitride ceramics have high hardness and high temperature strength properties. It can be used as cutting tools, grinding wheels and wire drawing dies, as well as raw materials for making tool materials and metal ceramic materials. Aluminum nitride ceramics also have excellent wear resistance. It can be used as a wear resistant part. Due to its high cost, it can only be used for parts with severe wear. Coating some easily oxidized metal or non-metal surfaces with AIN coating. This can improve its oxidation resistance and wear resistance; It can also be used as anti-corrosion coating, such as the processor of corrosive substances and the lining of containers.
Post time: Dec-03-2022