SSiC products
How can KSINO achieve such extraordinary achievements?
It is well known in the industry that the main advantages of SSiC technique are stable production process, stable batch, good product quality and low production cost. However, this technique requires high sintering conditions and raw materials. For a long time, reaction sintering process has been used to produce SiC products in China. This technique determines that there is total residual free silicon in the sintered green body, which will lead to the decrease of the strength and wear resistance of the sintered body. The most important is that free silicon cannot resist alkali and the corrosion of strong acid medium such as hydrofluoric acid. Therefore, its use is limited. This also led to the high-end market of SiC products being occupied by international leading enterprises.
The threshold of SSiC products is quite high. For example, its production equipment requires the sintering temperature over 2000℃ and inert atmosphere conditions.
The particle size, morphology, purity, oxygen content and pH of the powder should be considered. For instance, The particle size D50 is 0.5-0.6 μm; the purity must be above 99%......
KSINO has deeply studied and understood different molding technologies and the overall process of corresponding powder raw materials. Based on that, KSINO’s high-performance SiC products have such excellent properties as high mechanical strength, high hardness, wear resistance, high temperature resistance, strong acid and alkali corrosion resistance, oxidation resistance, thermal shock resistance, good thermal conductivity, extreme cold and extreme heat resistance, high temperature creep resistance and so on. We have accumulated a large number of high-quality customers in military industry, aerospace, nuclear power, metal smelting, high-temperature kiln, lithium ion battery production, powder metallurgy, ceramic chemical machinery, ultra-fine grinding, paper making, medicine and other fields.
Product series of SSiC products
SSiC product category |
Common product names |
High precision components for semiconductor process and optical mechanical equipment |
SiC crystal boat, mechanical arm, SiC base, triangular support, SiC sucker, etc |
Parts for glass forming |
SiC heating plate, SiC soaking plate, SiC mold, SiC mold sleeve |
Bulletproof ceramic bricks and ceramic plates |
SSiC bulletproof insert plate, SSiC bulletproof piece, SSiC bulletproof block |
Optical reflector components |
SSiC optical reflector |
Fluid Control Series |
SSiC seal ring, SSiC nozzle, SSiC impeller, SSiC shaft sleeve, SSiC plunger rod |
High temperature resistant parts |
SSiC burning rod, square beam and roller, SSiC crucible, SSiC burner sleeve, SSiC furnace tube, SSiC protective tube |
Chemical corrosion resistant parts |
SSiC protective sleeve, SSiC nozzle, SSiC head, heat exchanger tube sheet, SSiC tube bundle block, SSiC heat exchange plate, SSiC heat exchange tube, SSiC heat exchange control block, SSiC heat exchange block, micro reaction module |
Ion resistant etching parts |
SSiC CMP carrier, SSiC ICP carrier, SSiC PVD carrier, SSiC RTA carrier, SSiC carrier |
Wear resistant parts |
SSiC grinding cylinder, SSiC wear-resistant pipe, SSiC wear-resistant brick, SSiC wear-resistant plate, SSiC sealing ring, SSiC sandblasting nozzle, SSiC nozzle, SSiC grinding ball, SSiC bolt and nut |
SSiC bearing |
SSiC bearing, ceramic bearing ball |
Microchannel reaction unit |
SSiC reaction plate, SSiC reaction tube, SSiC micro reaction module |
SSiC tube |
Heat exchanger tube, heat exchanger ceramic tube |
SSiC shaft sleeve |
SSiC bearing sleeve, SSiC precision ceramic bearing, SSiC shaft sleeve |
Other customized products |
SSiC customized parts, SSiC customized ceramic parts |
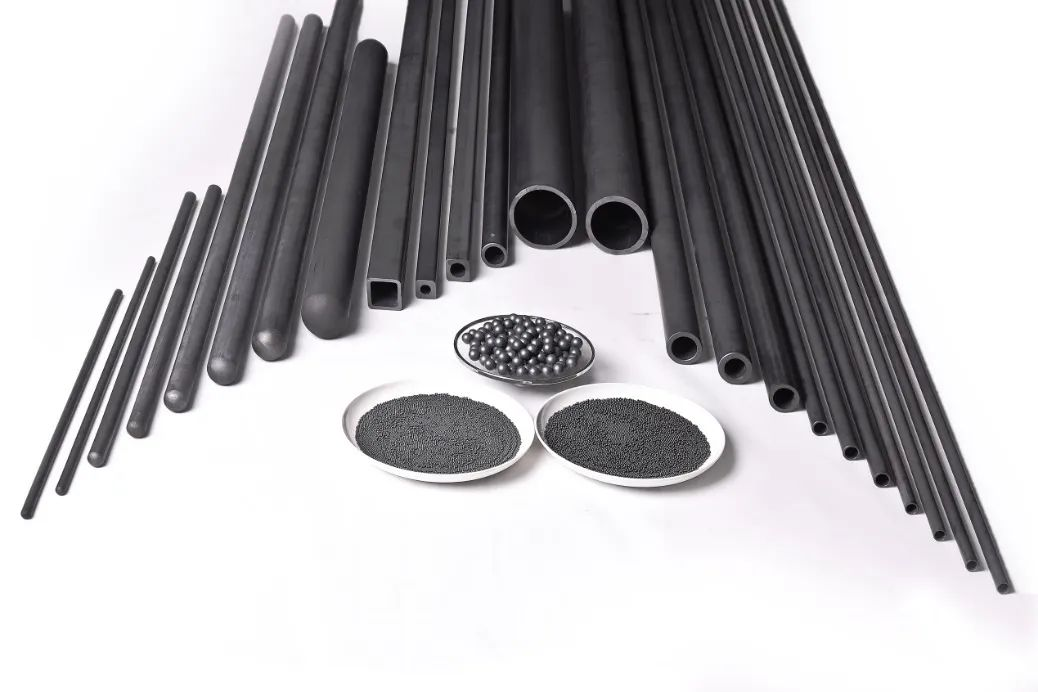
Typical molding technique and corresponding products
1. Dry-pressing
The dry-pressing is made by pressing the powder particles in the mold with a large pressure. Its essence is that particles are close to each other in the mold under the action of external force and firmly broken together and maintain a certain shape with the help of internal friction. This technique is mainly suitable for mechanical seal ring with low-cost in mass production, bulletproof sheet, integral bulletproof breast plate, sandblasting nozzle, shaft sleeve, plate, faucet valve sheet and other simple shaped parts.
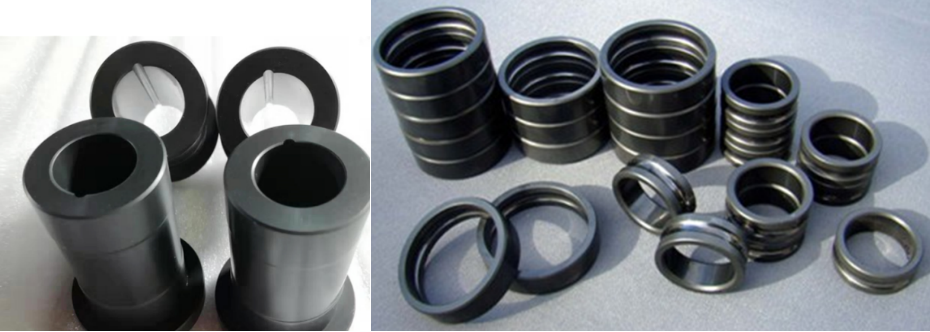
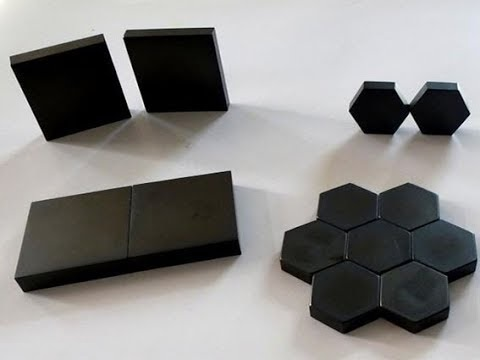
2. Isostatic compaction
Isostatic compaction is a molding method that uses the incompressibility of liquid medium and the property of uniform pressure transmission. Compared with the dry-pressing, the biggest characteristic of the isostatic compaction is that the powder material is in the state of three-way compressive stress.Therefore, the performance and quality of the formed parts are significantly improved. They are commonly used in the production of grinding barrels, block hole heat exchange parts, thermocouple protection tubes, pipes, heat radiation tubes, large plates, discs, etc.
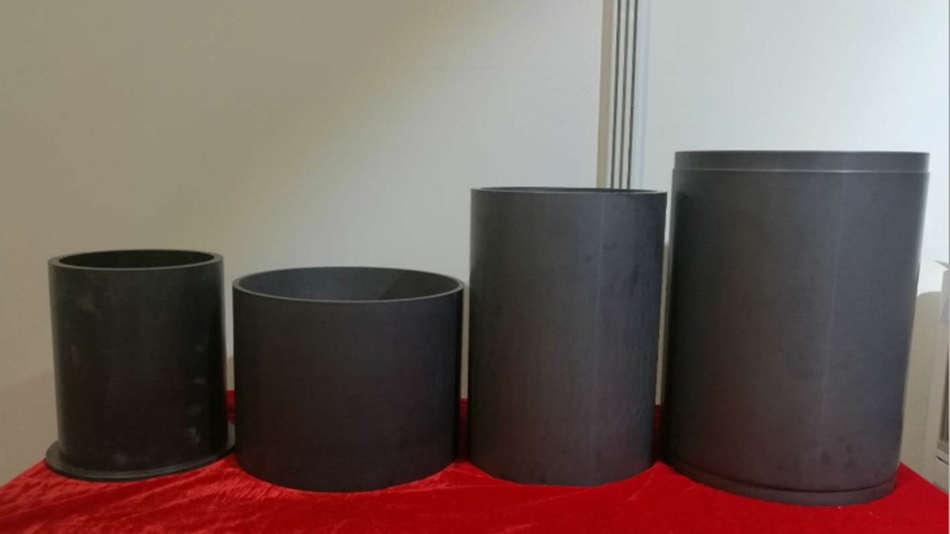
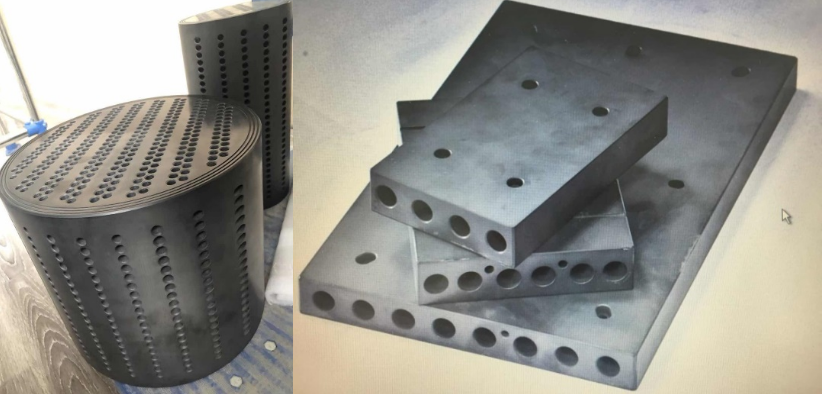
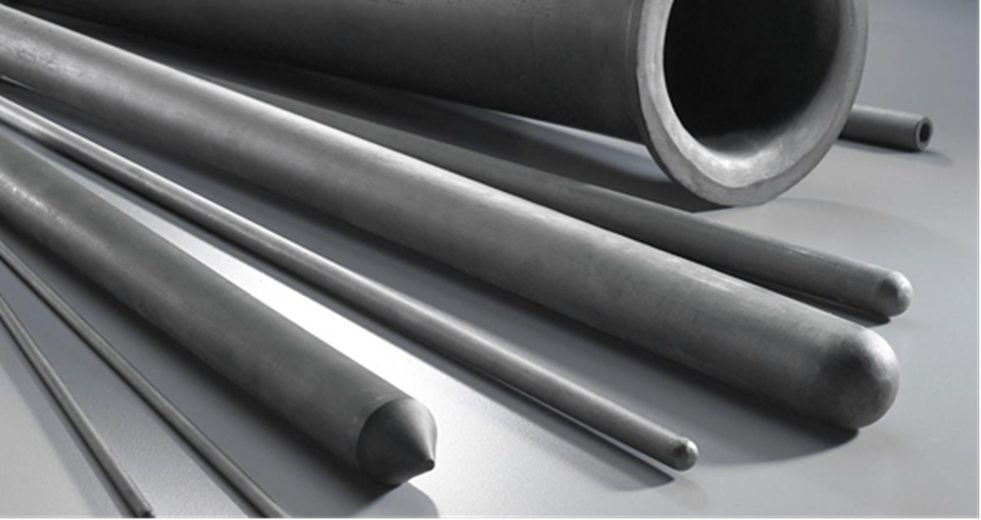
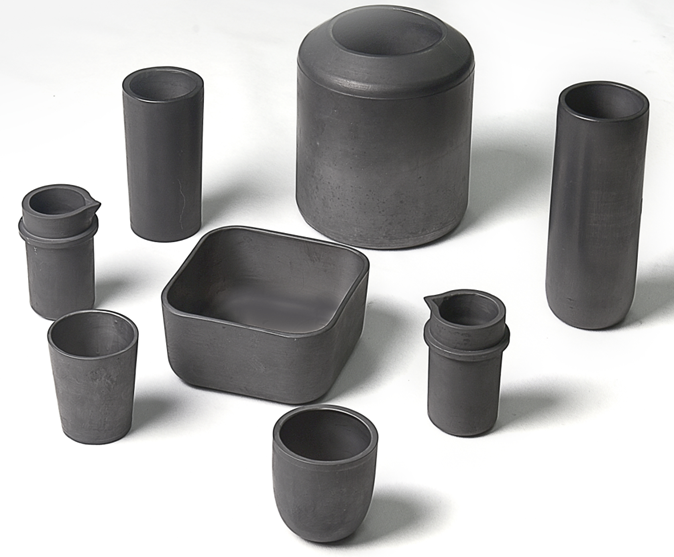
3. Slip Casting
Slip casting is achieved by injecting slurry into a porous mold made of gypsum abrasive tools. Depending on water absorption (solution) property of porous molds, the slip casting makes the slurry to be absorbed by the mold at the side close to the mold wall to form a uniform blank layer, which thickens with time going. When the required thickness is reached, the surplus slurry will be poured out. Finally, the preform body layer layer will continue to dehydrate and shrink to separate from the model. After being removed from the model, it will be the preform body. The slip casting can not only make ceramic products with complex shapes, but also be suitable to make large size ceramic products, such as thermocouple protection tubes, sagger crucibles, grinding barrels, sandblasting nozzles, pump shells, profiled pieces, etc.
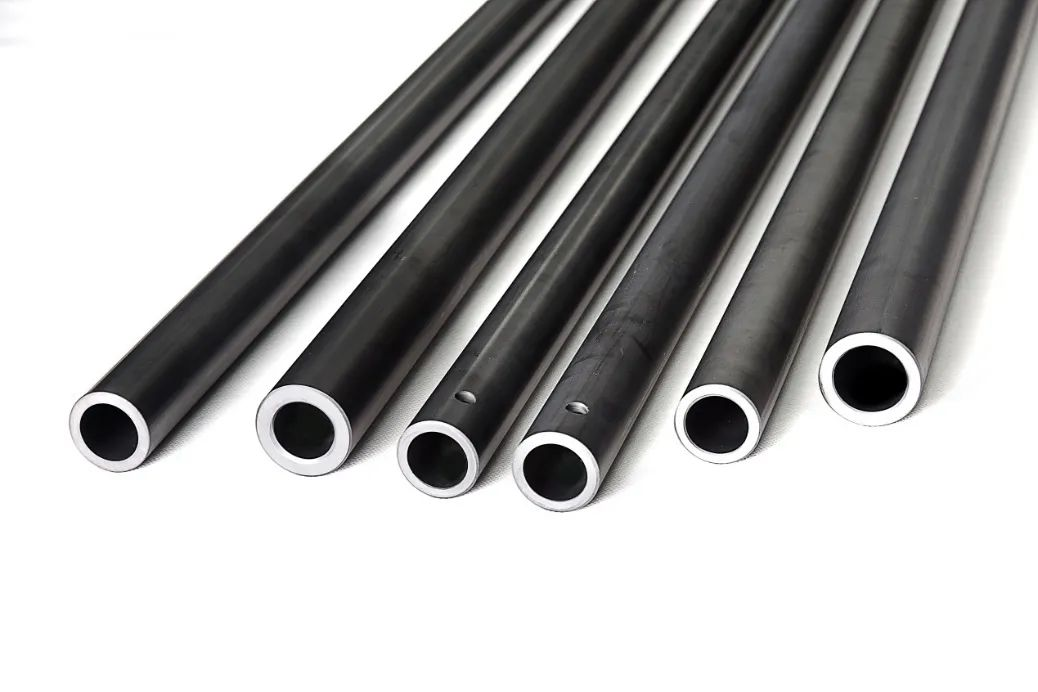
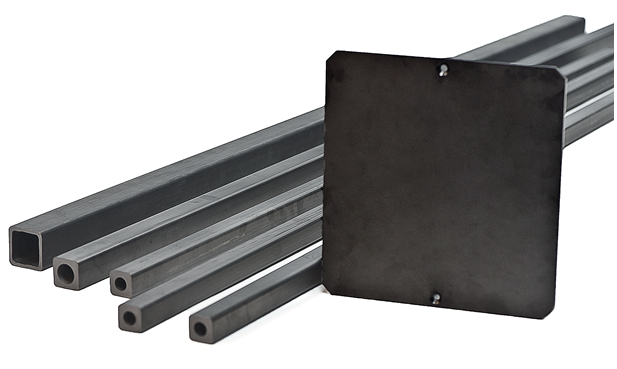
4. Extrusion molding
Extrusion molding is to put the vacuum refining mud into the high-pressure extruder and, under the influence of external force, extrude the green body into a certain shape through the extrusion nozzle, which is also called the die nozzle. The extrusion nozzle is the forming mold. It extrudes green bodies of different shapes by replacing the extrusion nozzle. This method is suitable for forming tubular parts with the same cross section. The extruded parts are almost unlimited in length direction, such as chemical heat exchange tubes, ceramic rods, square beams, DPF (exhaust gas filter), ceramic membranes, plates, etc.
Silicon carbide is so rare in nature that it was discovered very late. In the past three decades, with the progress of science and technology, silicon carbide has gradually burst into a dazzling light. However, SSiC products have become irreplaceable materials in many emerging application fields with excellent comprehensive properties. As a high-tech enterprise focusing on the SSiC business, KSINO has accumulated a lot of practical experience while serving customers. Our understanding and R&D ability of different application products are trustworthy!